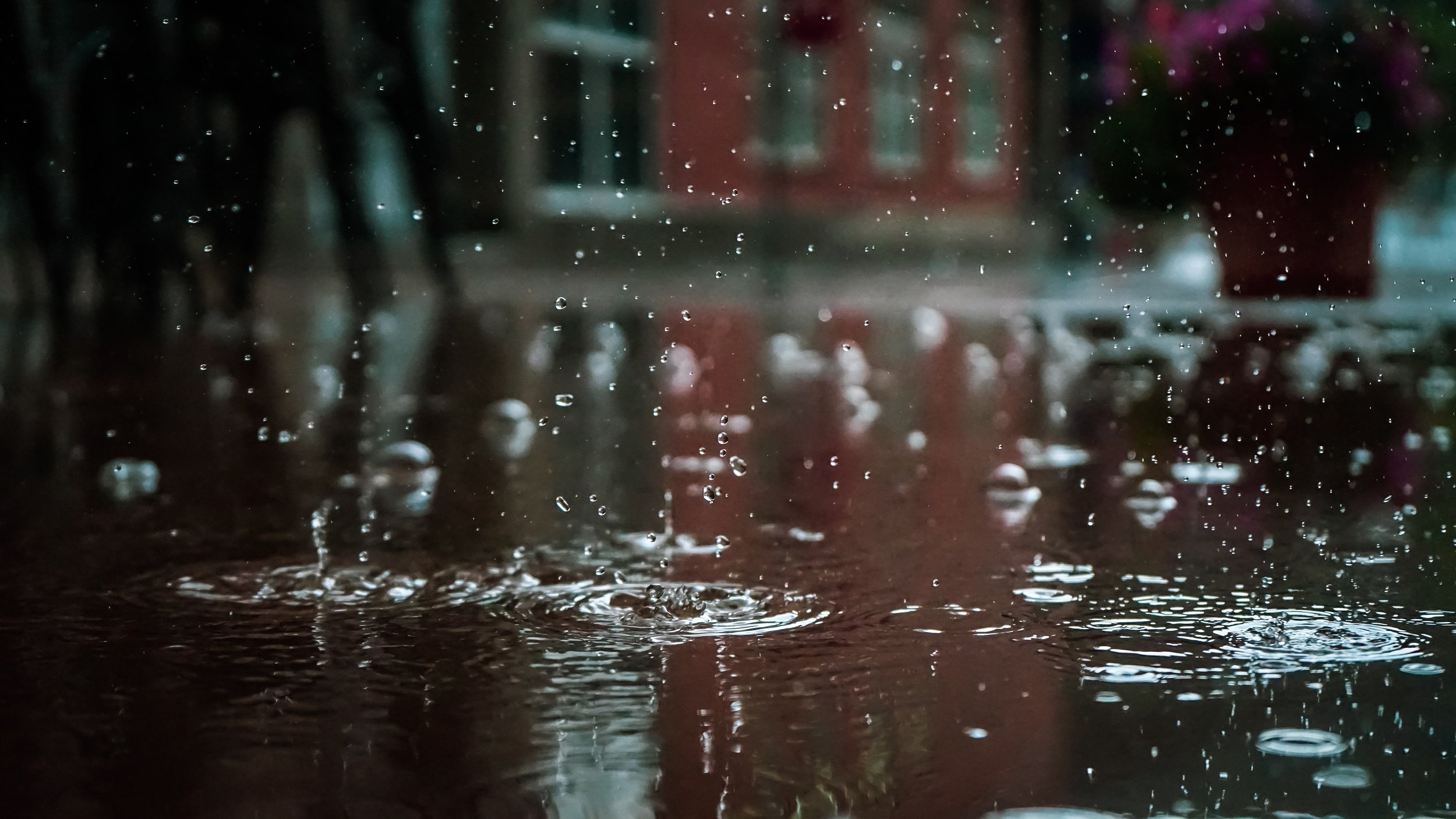
Principles of Stormwater Solutions

Stormwater is captured in a raw state, neither disinfected nor filtered.
Collected from surfaces exposed year-round to outdoor conditions, stormwater will contain high levels of particles and perhaps even debris. If it has been collected from hard surfaces with significant vehicular presence (driving or parking), petroleum hydrocarbons (VOC’s) are also likely to be present.
The essential requirement of stormwater technologies is to filter and disinfect captured rainwater to ensure it is safe for its intended applications.
No more, no less.
Ultraviolet light (UV) is among the simplest and most reliable of disinfection technologies, recognized as one that does not present complications or collateral risks.
Since UV relies on light waves, its efficacy is compromised by the presence of pathogen-shadowing particles in the water.
Therefore, the optimal sequence for a stormwater solution for many applications is:
1.Filtration to clarify the water sufficient to assure a high UV Transmittance (UVT) value.
2.UV applied to the filtered water to assure adequate disinfection.
3.Activated carbon filtration - if indicated by expected water conditions.
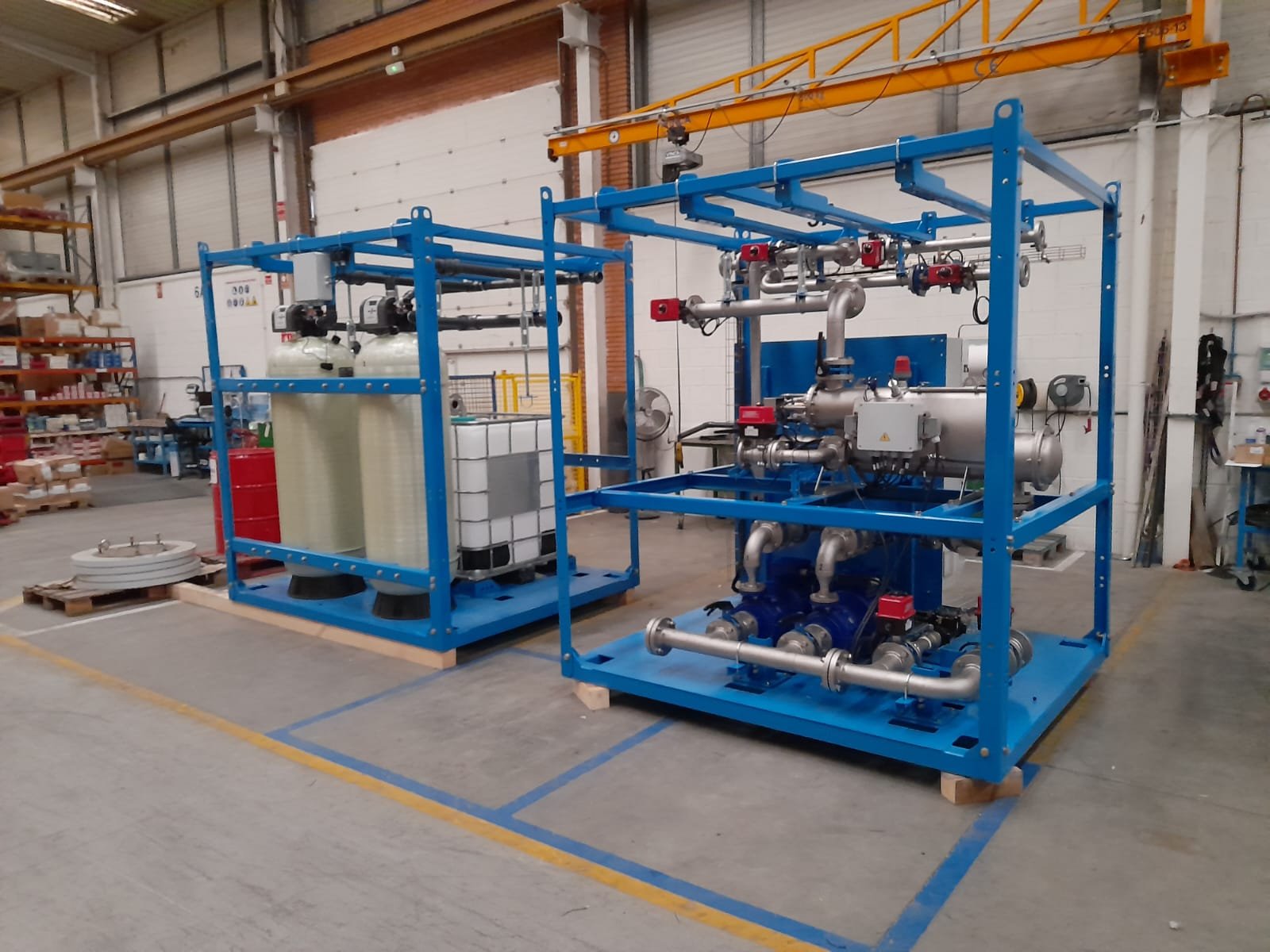
Here’s the fabricated solution at the factory.
Built as two skids that are joined together in the field, as shown.
Here’s a drawing of the same:
Plan view:
Additional drawings of skid one with stages one and two (filtration and UV):
Note this build uses a duplex pump skid, engineer-specified for redundancy on this particular project. If the expected water conditions did not indicate carbon media for reduction of hydrocarbons, this skid alone would suffice as the solution, with a simplex or duplex pump configuration.
Here are the drawings for the second skid with the duplex activated carbon media filtration system and surge tank.
Now let’s look at the P&ID for this same system:
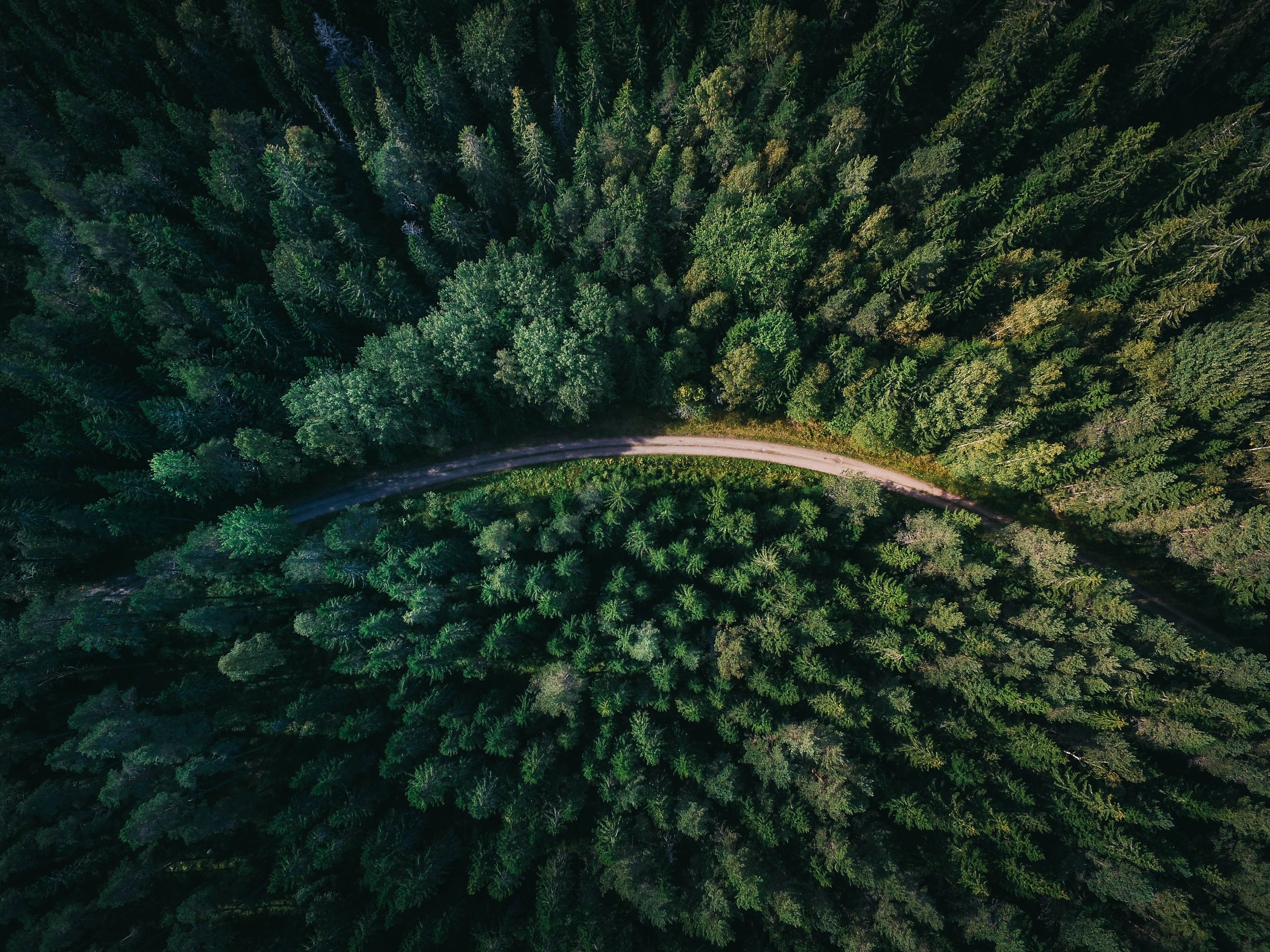
The underlying premise of our stormwater design is to prioritize simplicity, efficiency and reliability in the interest of a reduced footprint and lower cost.
When the core technologies are best in class, having fewer moving parts is a plus. For that reason, we urge engineers and other decision-makers to pay close attention to the benefits conferred, and quality of, the technologies included with an integrated solution.
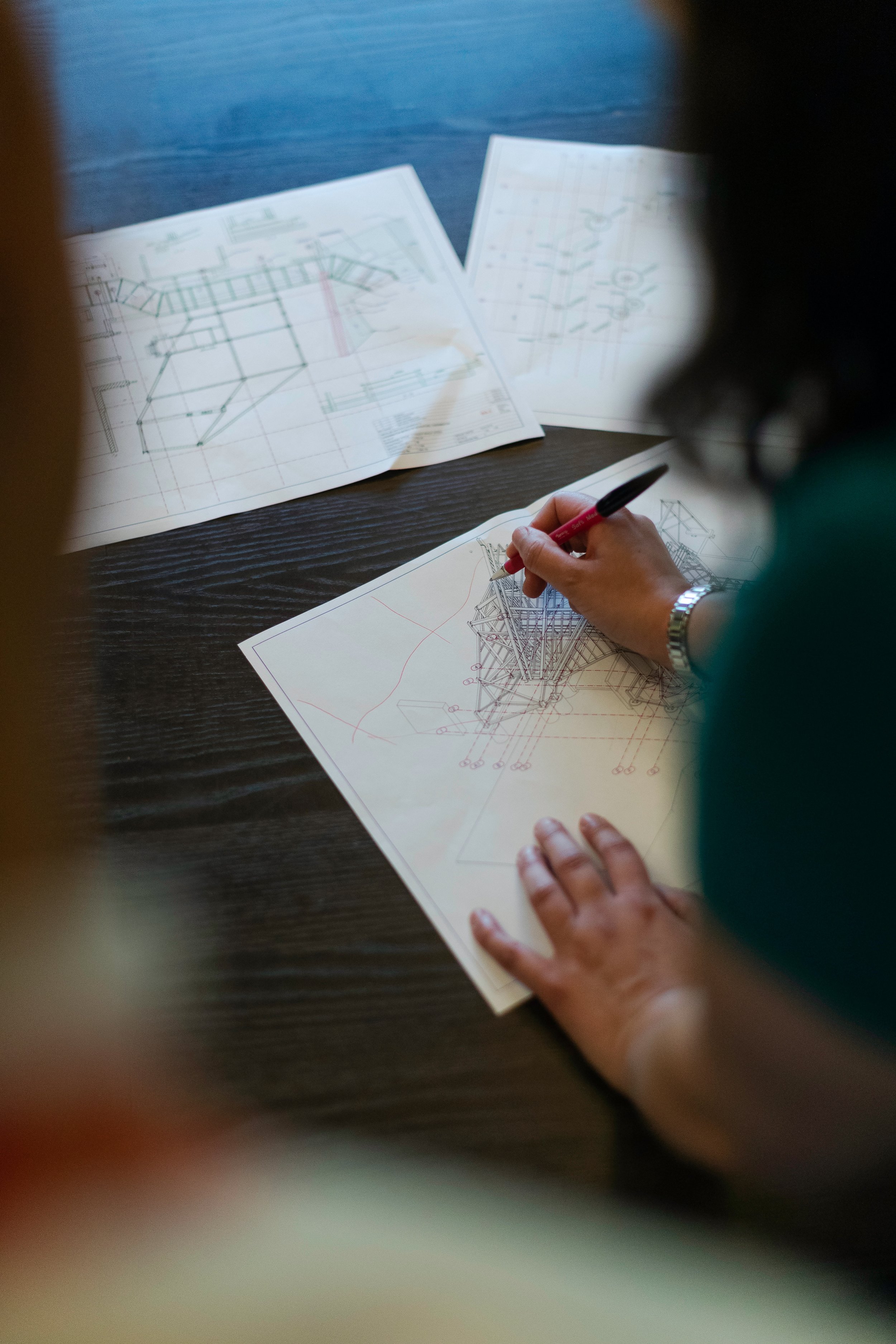
Finer filtration than required for the purpose of delivering an acceptable UV Transmittance (UVT) level has little more than academic value.
In most cases
50
micron
is the optimal filtration degree to apply before the UV. A finer degree than 50 generally has little impact on UVT, yet demands much more screen area (or media volume) to accommodate the given flow rate.
For applications requiring VOC reduction, automatic backwashing catalytic carbon filtration is the most effective technology.
Enough surface area to assure adequate contact time (water to media) is essential to meet a VOC reduction mandate.
For many applications, our Omicron 2900UV series -- a fully integrated screen filter + ultraviolet disinfection system built entirely at our factory in Monzon, Spain -- forms the core of our solutions.
Unlike other designs in which a systems integrator cobbles together a screen filter and a UV unit from separate factories, our solutions are constructed as completely integrated systems, with single manufacturer oversight and quality control from start to finish.
For very high flow rates, say >220 gpm, alternatively we may integrate a simplex or duplex high volume filter system with a high capacity UV unit in the interests of greater efficiency. These too are built and integrated at our factory.
Managing the probability factor
The most common application of the filtration + disinfection sequence is to supply a sidestream recirculation loop in and out of the retention tank.
Our skid-assembled systems therefore typically include a circulation pump and pressure sustaining valve. Alternatively, the pump(s) can be supplied external to the system (by others). In either case, screen filtration requires adequate pressure at the inlet to sustain the backwash cycles.
An efficient use of the pump on our skid is to supply enough pressure both for ongoing recirculation and flush cycles.
Ultraviolet light disinfection is highly effective but confers no downstream residual.
Therefore, the underlying theory behind a disinfection sidestream loop is that with sufficient recirculation frequency, nearly all pathogens in the detention tank water will be neutralized over the course of numerous passes of the total volume through the system.
Typically, water discharged from the filtration/UV system will be introduced into one side of the tank and exit from the opposite side, from where it returns for the next pass through the equipment.
This creates a robust recirculation loop to ensure that over time the entire tank volume is disinfected.
In order to take a step beyond relying on probability, we provide a tee at the outlet to assure that product water will be discharged to application directly from the system. This is done in order to completely assure pathogen-free water to application.
The system is thus set up to function both on a sidestream loop and for discharge direct to application.
For some applications, a disinfection residual is essential. For example, if the application supplied is a considerable distance away from our equipment. In this case, we usually apply a chlorination system instead of UV.
In other instances, it may be vital to assure absolute clear, colorless water for the intended application. In such cases, we replace screen filtration with an extremely fine media filtration system that delivers water at a low single-digit micron level below what screen filtration can provide.
This P&ID shows how both mandates are fulfilled through carefully considered design.
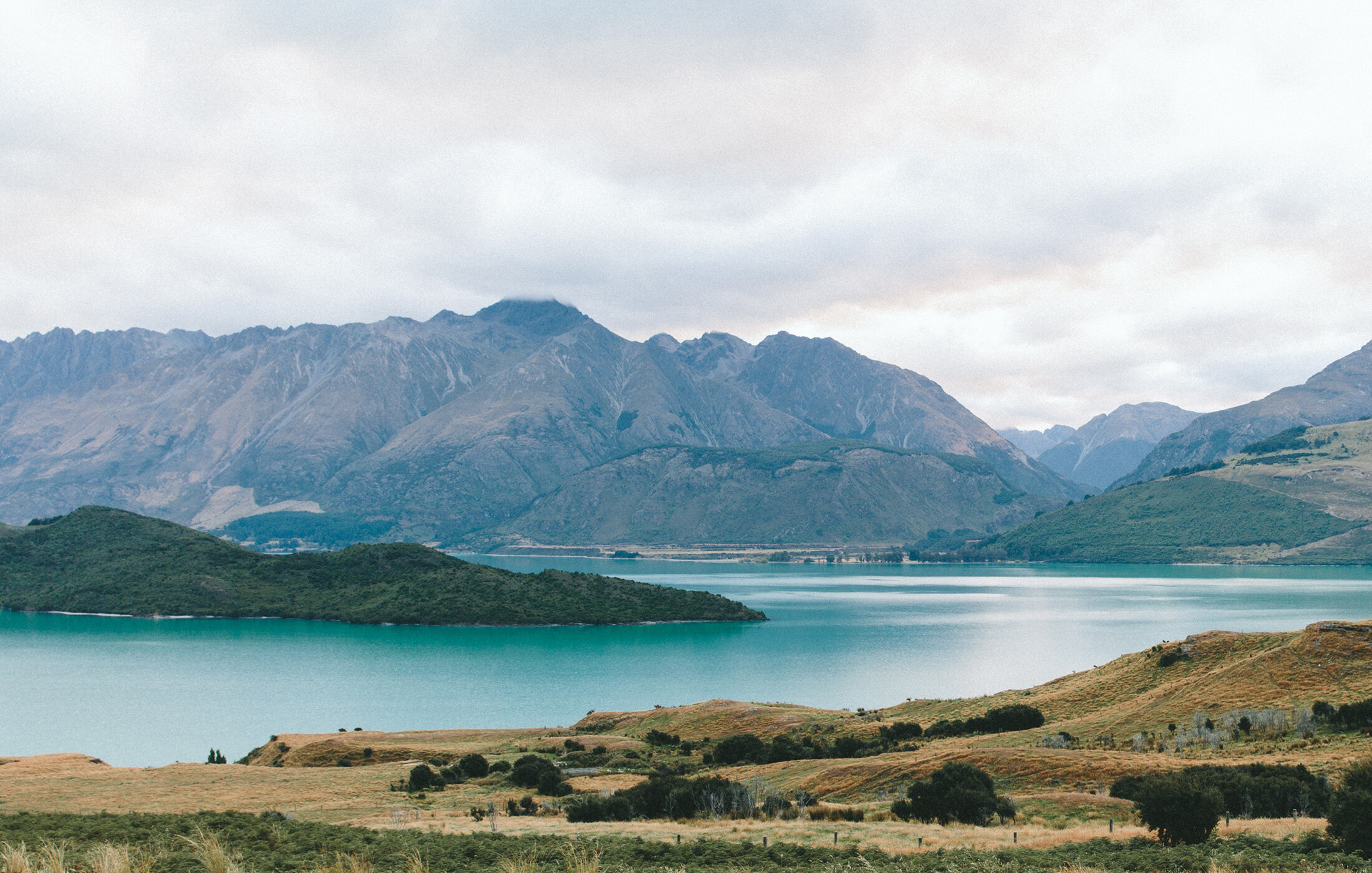